Plant Capacity
When we are playing BSG Online (or studying), we are hired and paid for managing plants. So, we need to understand what we are managing. It is common sense. We do not sell the factories. We need to learn how to manage them, build them, expand and upgrades, we are creating good products, and maintain good jobs for our workers.
From the Author's Guides, we find this point useful, actually, we create good strategies based on this points:
User all the capacity we have every year, for both Branded Production and Private Label. Because when we produce all capacity, we can reduce cost, get higher margins, charge lower price, have higher market shares, so we increase EPS and Image rating.
Making private-label shoes for chain retailers allows a manufacturer to use plant capacity more efficiently. For example, a manufacturer selling only 5.5 million pairs of branded shoes with plant capacity of 6 million pairs (7.2 million pairs with maximum use of overtime) can reduce overall costs per pair by utilizing some or all of its unused capacity to produce private-label shoes. The added production volume from being a successful low-bidder to supply private-label shoes to chain retailers helps spread fixed costs over more pairs and can improve overall financial performance (provided the price received for producing the private-label shoes is above the direct costs per pair)
2. The cost in NA factory will be higher when approaching year 14-15 and later. So, we can build a new factory in LA, and same time, we expand factory in AP. Some groups do this very from Year 11. It is OK, we can do that. (Note that when most of team do so, the competition will be tough).
But locating most of the company’s production in Asia-Pacific and/or Latin America has two potentially significant disadvantages. Tariffs have to be paid on footwear exported from Asia-Pacific plants to markets in Latin America ($6 per pair) and Europe-Africa ($4 per pair); likewise, tariffs have to be paid on footwear exports from Latin American plants to markets in Europe-Africa ($4 per pair) and the Asia-Pacific ($8 per pair)—it’s uncertain whether tariffs in future years will rise or fall and by how much. Also, all companies are subject to unfavorable year-to-year exchange rate fluctuations in shipping footwear from one region to another (as discussed below). One way to guard against adverse changes in tariffs and exchange rates is to maintain a production base in each of the four geographic regions and rely upon those plants to satisfy demand for the company’s branded footwear in their respective region. It remains to be seen how companies will weigh the pros and cons of locating plant capacity in one region versus another.
We can check the decisions about Plant as follows:
1. Check total market supply and demand.
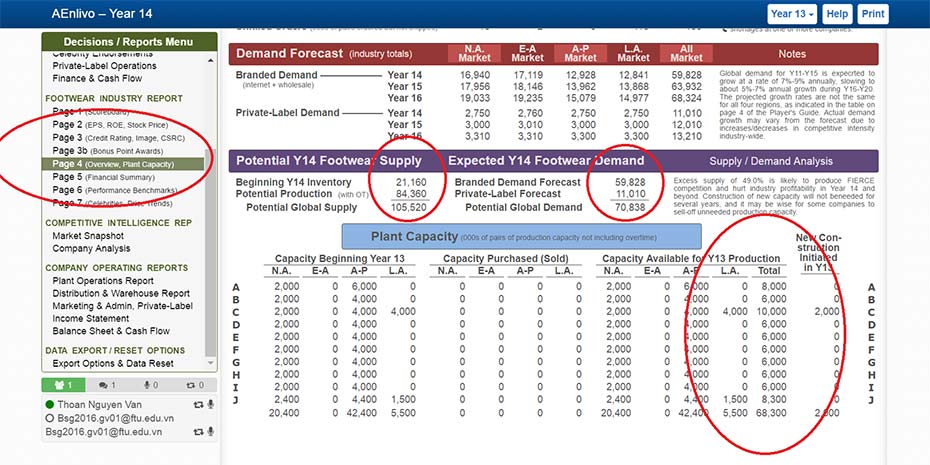
The Plant Capacity page involves deciding whether to (1) add new shoe-making capacity (by constructing new plants, expanding existing plants, or by purchasing used footwear-making equipment if any is available), (2) upgrade production features at one or more existing plants or (3) permanently sell-off all or part of the production capacity of an existing plant. Adding New Production Capacity. You and your co-managers have the option at any time to expand the capacity of the 2 million-pair North American plant and/or the 4 million-pair Asia-Pacific plant. You can also establish a production base in the other two geographic areas. New plants in Europe and Latin America may be constructed in capacities ranging from a minimum of 1 million pairs annually to a maximum of 2 million pairs per year (not counting overtime); new plants can be expanded later as needed. The construction of new plants and plant expansions takes 1 year to complete. Thus, a decision to build a new plant or expand an existing plant in Year 11 means the plant or plant expansion will come on line ready for full production at the beginning of Year 12. There is no limit on the number of times that an existing plant site can be expanded. The maximum amount that an existing plant can be expanded in any one year is 50% of existing plant capacity—all plant expansions must be in increments of 100,000 pairs. The North American and Asian-Pacific plants and any new plants built in Europe-Africa or Latin America can be expanded over time up to a limit of 12 million pairs of total production capacity (not counting overtime) at each plant site. Therefore, the company is limited to a maximum of four different plant sites (one in North America, one in Asia-Pacific, one in Europe-Africa, and one in Latin America) and a maximum of 48 million pairs of capacity--far in excess of the total capacity you will need. All costs for added capacity—newly-constructed plants or existing plant expansions—must be paid for in the same year as the decision to build or expand is made. The cost of new capacity varies according to the year ordered; scale economies and learning/experience curve effects are allowing the makers of new state-of-the-art footwear-making equipment to reduce their prices at the rate of 2.5% annually. The announced price for new footwear production capacity in Year 11 is $5 million per 100,000-pairs of capacity, but the 2.5% annual declines will result in a cost of only $4.3 million per 100,000 pairs of capacity by Year 16. Hence, delaying the decision to add new capacity until it is really needed has the advantage of lowering the capital investment in new facilities and equipment. You can always see what the current costs of new capacity will be in any particular year by entering numbers for the desired amount of new capacity and observing the resulting capital outlays shown at the bottom of the decision entry page. New production capacity is considered to have a service life of 20 years and the capital costs are depreciated on a straight-line basis at the rate of 5% annually.
Purchasing Used Plant Capacity.
The opportunity to purchase used, but newly-reconditioned, plant capacity at prices 20% below the cost of new construction may arise at some point. Used capacity becomes available for purchase when a company in your industry elects to sell off production capacity at one or more of its plants to merchants who specialize in buying used plant capacity in increments of 100,000 pairs and then reselling it to interested footwear companies. The amount of any used capacity that is available from these merchants, the geographic area in which it is available (plant capacity cannot be transported from one geographic region to another), and the prices of such capacity are shown on the Purchase Capacity page (see the Purchase Capacity button near the top of the Plant Capacity page). All purchases of used capacity occur on a first-come basis. The advantage of buying used capacity is that it can be purchased and made available for use virtually overnight (purchased capacity becomes available in the same year that it is purchased). However, if your company does not have a plant in the geographic region where you are considering purchasing used capacity, then the minimum-size purchase is 1 million pairs; this is because plants smaller than 1,000,000 pairs of annual capacity tend to have prohibitively high production costs and usually cannot be cost competitive against larger-scale plants. Because used capacity is reconditioned, it is considered to have a service life of 20 years. The capital cost is depreciated on a straight-line basis at the rate of 5% annually
We can purchase plants in AP, LA, if you like, we can even purchase factories, in NA but be careful.
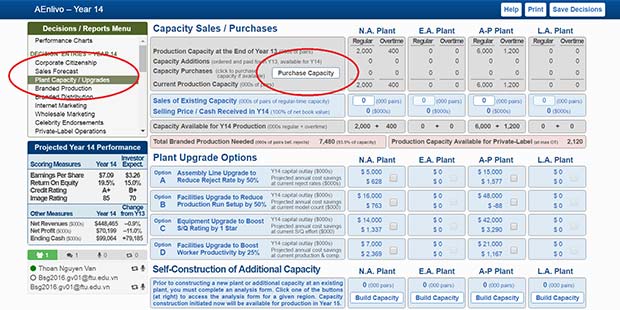
Tips
We select the capacity we can purchase, often we buy all from LA and AP available. But most of the team do not sell the factories in here.
The game often is processed at 23.59, so that other teams will login to check if someone sells the factories, we need to login early of we want to buy the available factories, because first come, first serve.
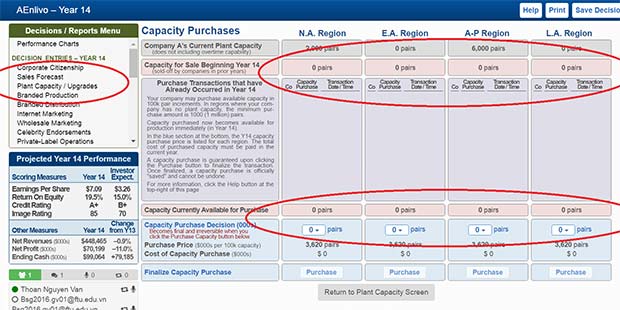
Selling Some or All of a Plant.
The Game provide this Function, but DO NOT do this, only when you try everything, and can not maintain Net Profit !!!
Some group play a trick by expanding AP and LA factories fast and sell NA factory to keep total Equity lower, but be careful when doing so.
The merchants of used plant capacity stand ready to purchase all or a portion of the capacity in any of your plants at a price equal to your company’s net book value (this value is shown in your company’s Plant Operations Report as “Net Investment in Year X Capacity” and will display on the page immediately below an entry to sell-off existing capacity). Capacity must be sold in 100,000- pair increments. To sell any of the capacity at any of your company’s plants, simply enter the amount of capacity that you want to sell in the indicated spaces on the Plant Capacity page. The money from the sale is received immediately and the capacity is removed immediately (that is, in the year for which the decision entries are made). Special Note: Keep in mind that when you sell off plant capacity (either part or all of a plant) you are permanently selling the facility. The amount of capacity that you choose to sell off is removed immediately and does not return the following year.
Plant Capacity / Upgrades
We have two plants in year 11, and growth rate of market is about 5-7%, during 10 years from year 11 to year 20 we will need to double may be triple production capacity. Decide right time to upgrade factories or expand or build a new factory is a key to success.
It is good to expand or build on the existing plants. Often in AP because of lower labor cost. We can look at cost per pair of shoes in years 13-14 and later to see this.
Never sell our factory. It is both in game and in life if we can avoid the worst situation. We do not want to laid off thousands of workers. And also we want to win the game, so the most powerful things we are having is our plants. How can we compete without plants. So do not sell the plants, again. If we have too much extra capacity we can use that for Private Label markets. We can lower price, increase advertising, many ways to sell more. And, bottom line shows that the Net Profit depends on Margin and Number of Products sold.
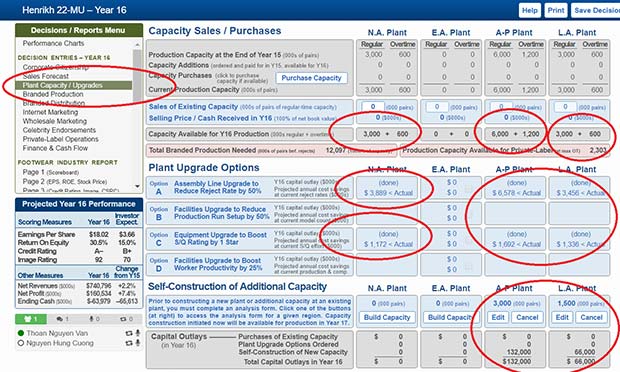
In this table, we need to select 2 Options to upgrade our plants. If we follow High S/Q, the Option C is most appropriate, because it saves a lot of cost when we produce higher Stars.
If we follow the large number of models, high capacity, so the Production Run Setup Reduction upgrade is good because it saves cost when we produce large number of products.
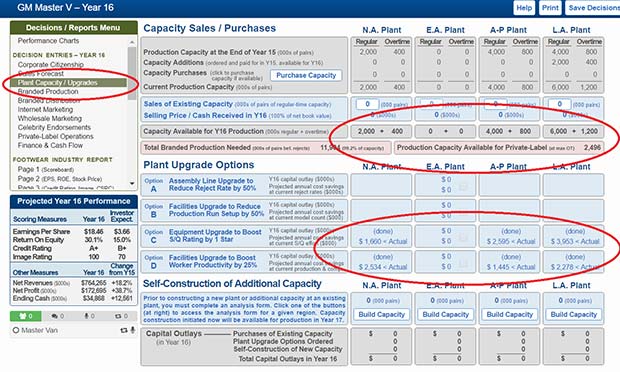
In conclusion, we need to look at Market Report - Page 4 to see the Total Market Demand vs Total Market Supply, if the surplus is about 20%, we can build a new factory.
Also, this is a competition game, so if we do not build or expand factories, our competitors will do, therefore, it is better to make this decision in advance. Higher capacity will lower cost of productions, therefore we can have higher margins.
Do not build factory in EA, because later years, cost of production in this continent is higher, highest in all 4 markets.
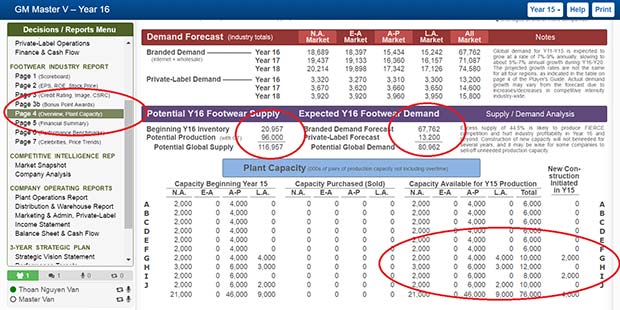
Often, we expand factory in AP then we can build new in LA, if not needed we can sell factory in NA (do not recommend or only when necessary).
Take a good care of ROE when building new factory, because too much too high Equity can lower the ROE if Revenue can not increase as much as capacity or Total Equity.